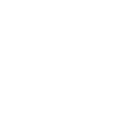 |
الوان ثابت در یک نگاه :
شرکت دانش بنیان الوان ثابت در سال1361در 45 کیلومتری شهرستان همدان در جاده همدان – تهران به عنوان بزرگترین سنتز کننده رنگ و مواد شیمیایی در خاورمیانه با پوشش صنایع نساجی و چرم تاسیس شد و در چهار گروه رنگ های نساجی اسیدی، مستقیم، راکتیو وخمیر پیگمنت در سال 1375 مورد بهره برداری قرار گرفت.
|
سپس در سال 1383 با ارتقاء دانش فنی تولید و جذب کارشناسان کارآزموده کیفیت محصولات تا سطح استانداردهای بین المللی ارتقاء داده شد و سالانه بیش از 100 نوع از رنگ های اسیدی، راکتیو، مستقیم، خمیر پیگمنت و مواد تعاونی نساجی ، چرم و کاغذ را برای مشتریان بی شمار در سراسر کشور و برخی کشورهای همسایه تامین می نماید.

راهنمای خرید از الوان ثابت استخدام در الوان ثابت ثبت شکایات نظرسنجی درباره ما تماس با ما